Introduction
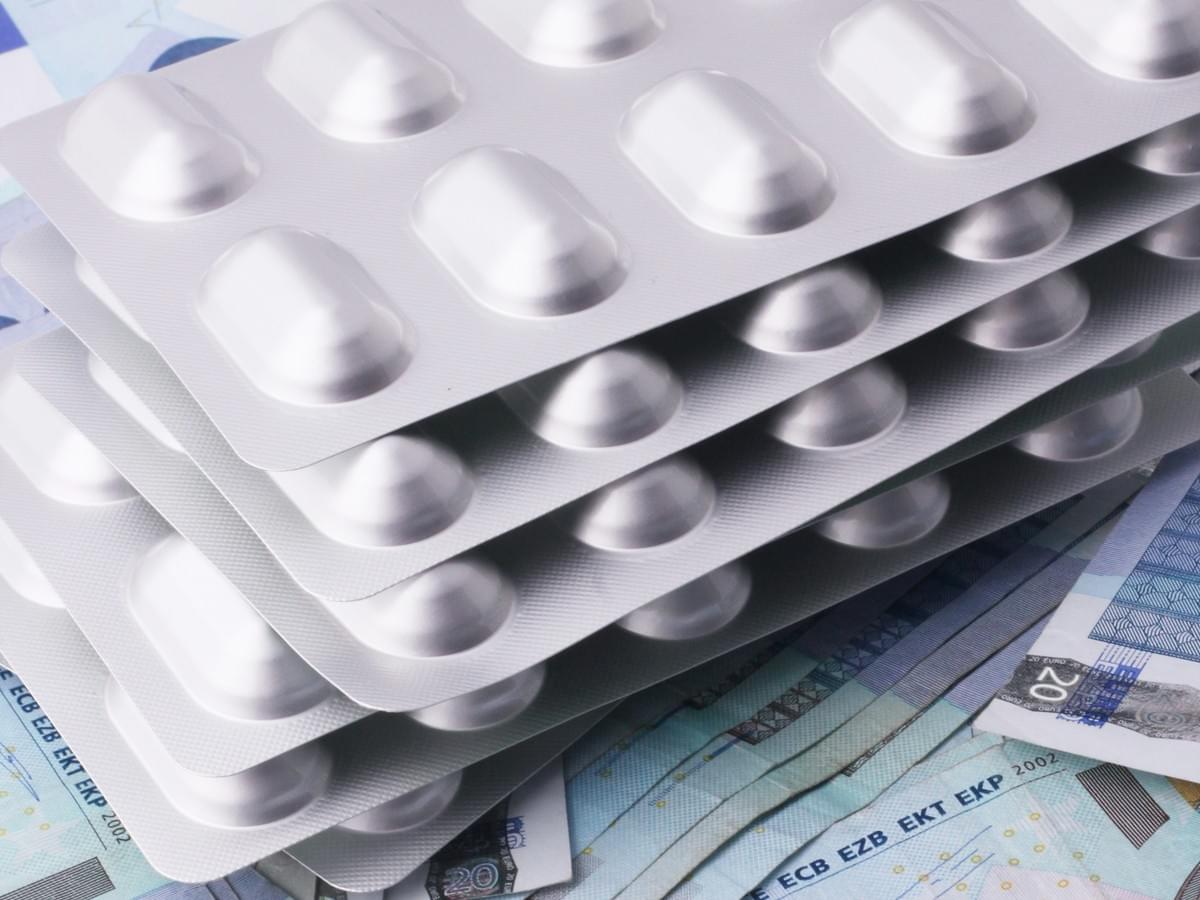
In the realm of pharmaceuticals, medicinal blister packaging stands out as a crucial component in ensuring the safety and efficacy of medications. This innovative packaging method not only protects sensitive products from environmental factors but also provides convenience for users. Understanding the nuances of aluminum blister adhesive is essential for maximizing the benefits of this packaging solution.
Understanding Medicinal Blister Packaging
Medicinal blister packaging involves encasing individual doses of medication in a pre-formed plastic cavity, typically sealed with a backing material such as aluminum foil. This type of packaging is designed to protect against moisture, light, and other external elements that could compromise drug integrity. Moreover, it allows patients to easily access their medications while maintaining accurate dosage control.
The Role of Aluminum Blister Adhesive
Aluminum blister adhesive plays a pivotal role in ensuring that the various components of blister packs adhere securely to one another. The effectiveness of these adhesives determines how well the package will protect its contents from external factors while remaining user-friendly. When considering what is the best adhesive to bond aluminum to aluminum, it's essential to focus on properties such as temperature resistance, moisture barrier capabilities, and overall durability.
Key Benefits of Blister Packaging
Blister packaging offers several key benefits that make it an attractive choice for pharmaceutical companies and consumers alike. First and foremost, it enhances product protection by minimizing exposure to air and humidity—two common culprits in medication degradation. Additionally, blister capsule packaging using PTP aluminum foil sealing allows for tamper-evident seals that bolster consumer trust while providing clear visibility of each dose.
What is Blister Packaging?
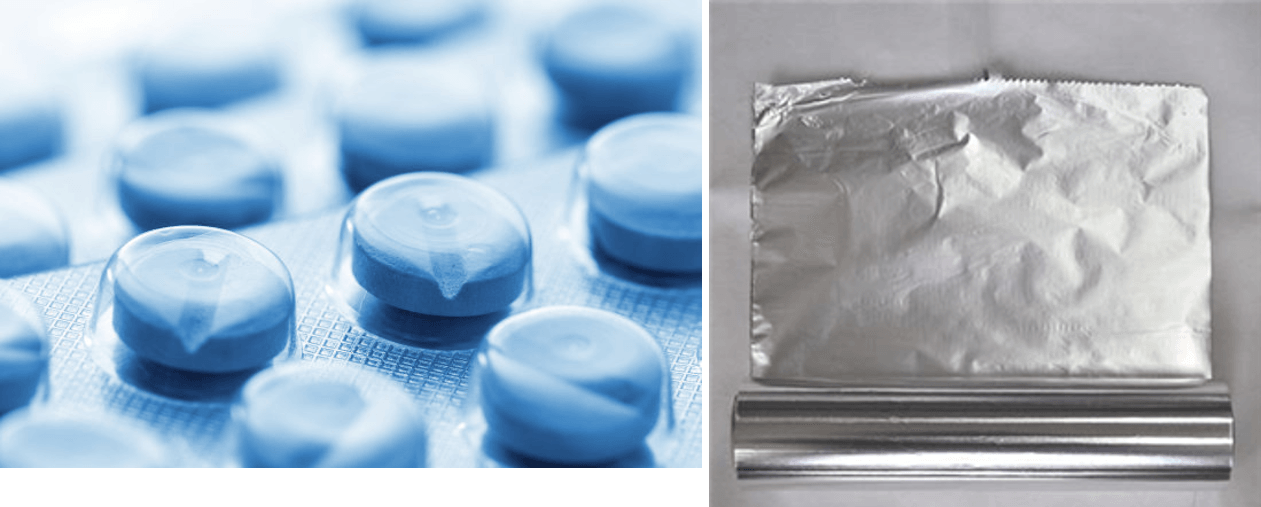
Blister packaging is a widely used method for enclosing products, particularly in the pharmaceutical industry. It involves creating a sealed unit that protects and preserves the contents, typically tablets or capsules. This type of packaging not only enhances product visibility but also provides essential barriers against moisture and contamination.
Overview of Blister Packaging Types
There are several types of blister packaging, each tailored to meet specific product requirements. The most common types include face seal blisters, full seal blisters, and clamshells. Each design serves unique purposes; for instance, face seal blisters expose part of the product while providing easy access, whereas full seal blisters offer maximum protection by completely encasing the item.
Differences Between Alu Alu and Blister
When discussing blister packaging, it's crucial to understand the difference between alu alu and traditional blister types. Alu alu refers to aluminum-to-aluminum sealing, which offers superior protection against moisture and light compared to standard plastic-based blisters. In contrast, traditional blister packs often use PVC or PET materials that may not provide the same level of barrier properties as alu alu options.
Materials Used in Blister Packaging
The materials used in blister packaging are critical for ensuring product safety and integrity. Commonly utilized materials include PVC (polyvinyl chloride), PET (polyethylene terephthalate), and aluminum foil—often referred to as blister foil—which is known for its excellent barrier properties. The choice of material directly impacts factors like shelf life and overall effectiveness; thus understanding what material is used for blister packaging can significantly influence manufacturing decisions.
The Science Behind Aluminum Blister Adhesives
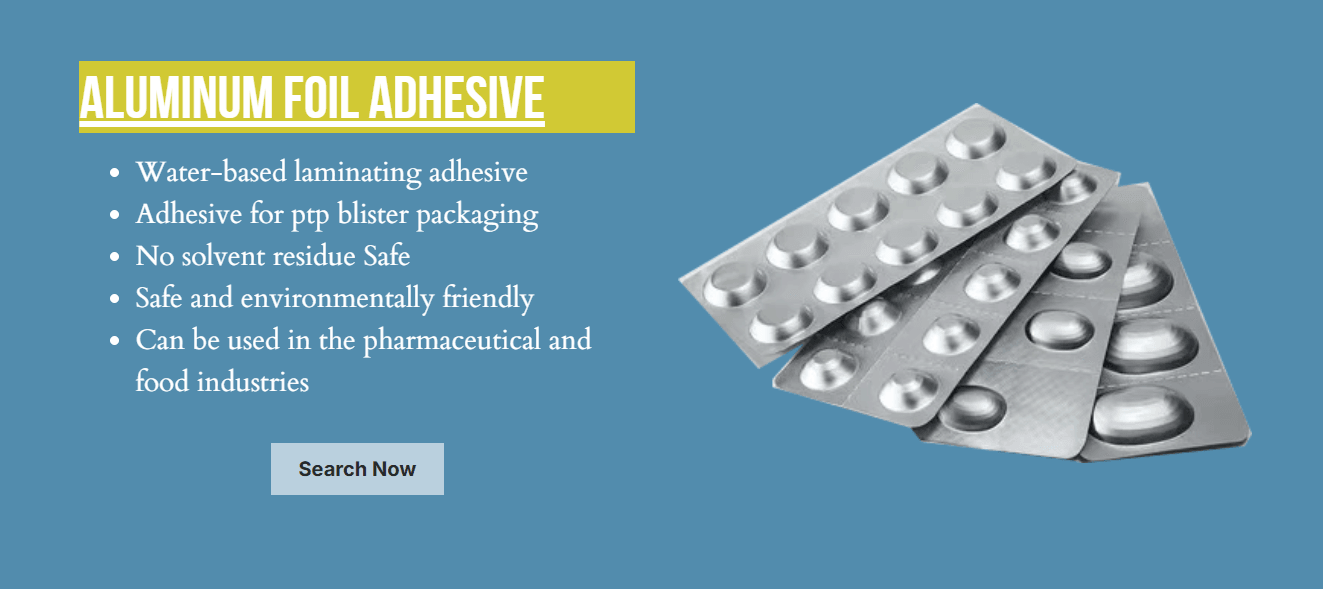
Understanding the science behind aluminum blister adhesives is crucial for anyone involved in pharmaceutical packaging. These adhesives are specifically formulated to bond aluminum to aluminum, ensuring that the blister packaging remains secure and effective in protecting its contents. The right adhesive can enhance product integrity, extend shelf life, and improve user experience.
How Aluminum Blister Adhesive Works
Aluminum blister adhesive operates through a combination of chemical and physical bonding mechanisms. When applied to the surfaces of aluminum foil, the adhesive forms strong molecular connections that resist peeling and tearing. This robust bond is essential for maintaining the integrity of blister packaging, particularly when it comes to protecting sensitive medications from moisture and air.
In terms of application, aluminum blister adhesive is often used in processes like blister capsule packaging with PTP (push-through) aluminum foil sealing. This method allows for easy access to individual doses while keeping them securely sealed until needed. Ultimately, understanding how these adhesives work can help manufacturers select the best adhesive for their specific needs.
Key Properties of Effective Adhesives
Effective aluminum blister adhesives possess several key properties that make them suitable for use in pharmaceutical applications. First and foremost is adhesion strength; an ideal adhesive must provide a durable bond between materials without compromising their integrity over time. Additionally, resistance to environmental factors such as temperature fluctuations and humidity is critical in ensuring long-lasting performance.
Another important property is compatibility with various materials used in blister packaging—such as PVC or PET—while still being able to bond aluminum effectively. Furthermore, non-toxicity is paramount; any adhesive used must be safe for medical applications since it may come into contact with pharmaceuticals directly or indirectly.
Common Applications in Pharmaceutical Industry
In the pharmaceutical industry, aluminum blister adhesives find wide-ranging applications primarily due to their effectiveness in protecting medications from external elements like moisture and light. They are commonly used in both alu alu (aluminum-to-aluminum) and traditional blister packs—each serving different purposes based on product requirements.
For instance, alu alu packs are known for providing superior protection compared to standard blisters because they utilize two layers of aluminum foil; this raises questions like What is the difference between alu alu and blister? The answer lies mainly in their protective capabilities: alu alu offers enhanced barrier properties ideal for sensitive drugs requiring maximum stability.
Aluminum blister adhesives also play a vital role in ensuring compliance with regulatory standards by providing tamper-evident features that enhance patient safety—a critical aspect given today’s stringent regulations surrounding pharmaceuticals.
Exploring Chemix's Water-Based Resin Solution
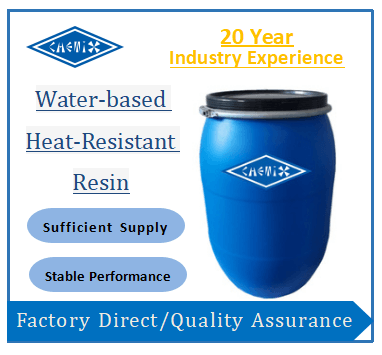
In the quest for effective aluminum blister adhesives, Chemix's water-based resin solution stands out as a remarkable innovation. This type of adhesive not only provides strong bonding capabilities but also caters to the growing demand for environmentally friendly products in the pharmaceutical industry. As we delve deeper, we'll explore its features, environmental benefits, and specific applications in aluminum blister adhesive formulations.
Features of Water-Based Resin
Chemix's water-based resin showcases several impressive features that make it an ideal choice for aluminum blister adhesive applications. First and foremost, it offers excellent adhesion properties that ensure a secure bond between aluminum components, which is crucial when considering what is the best adhesive to bond aluminum to aluminum. Additionally, this resin is designed to be user-friendly; it can be easily applied and cured without requiring complex processes or equipment.
Another notable feature is its versatility; Chemix's water-based resin can be adapted for various materials used in blister packaging, including PVC and PVDC films. This adaptability makes it suitable for different types of blister packaging solutions while ensuring compliance with industry standards. Moreover, the formulation allows for quick drying times and high-performance results that meet the rigorous demands of pharmaceutical applications.
Environmental Benefits of Chemix's Solution
One of the standout aspects of Chemix’s water-based resin solution is its commitment to sustainability and reduced environmental impact. Unlike solvent-based adhesives that emit harmful volatile organic compounds (VOCs), this water-based alternative significantly lowers emissions during application and curing processes. This aligns perfectly with global efforts to minimize pollution and promote greener manufacturing practices in industries like pharmaceuticals.
Furthermore, using a water-based resin contributes to safer working conditions for employees involved in production processes related to aluminum blister adhesive applications. The non-toxic nature of these resins means fewer health risks associated with exposure compared to traditional solvents. By choosing this innovative solution, manufacturers not only enhance their product quality but also take an important step toward eco-friendliness.
Applications in Aluminum Blister Adhesive
The versatility of Chemix’s water-based resin extends into various applications within the realm of aluminum blister adhesive systems used in blister capsule packaging techniques such as PTP aluminum foil sealing. Its strong bonding capabilities make it ideal for securely sealing capsules while maintaining product integrity during transportation and storage—critical factors when considering what material is used for blister packaging.
Additionally, this innovative solution can be employed effectively across different types of blister packs beyond traditional formats—addressing inquiries like what is the difference between alu alu and blister? By adapting to both alu alu (aluminum on both sides) and standard blisters (plastic backing), Chemix’s resin ensures flexibility across multiple product lines while maintaining high performance in adhesion strength.
In summary, Chemix’s water-based resin solution not only meets stringent requirements for bonding efficiency but also promotes environmental responsibility within pharmaceutical manufacturing practices involving aluminum blister adhesives.
Selecting the Right Adhesive for Aluminum
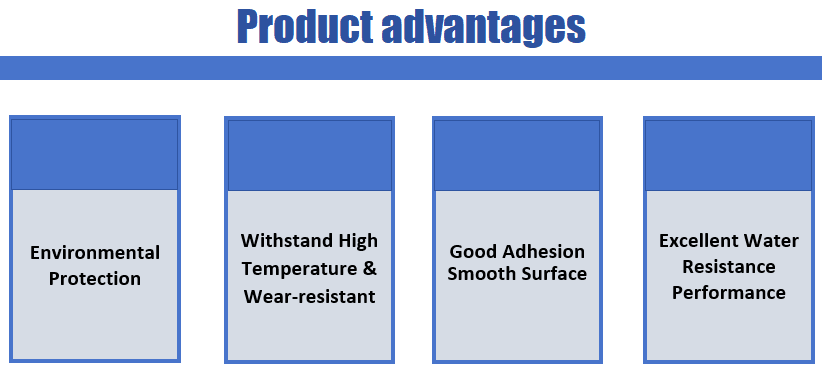
Choosing the right aluminum blister adhesive is crucial for ensuring product integrity and efficacy in pharmaceutical applications. Various factors come into play when selecting an adhesive, including compatibility with materials, environmental conditions, and regulatory requirements. Understanding these factors can significantly enhance the performance of your blister packaging.
Factors to Consider in Adhesive Selection
When selecting an aluminum blister adhesive, several critical factors must be evaluated to ensure optimal performance. First, consider the material compatibility; adhesives should bond well with both aluminum and any other materials used in blister packaging, such as PVC or PVDC films. Additionally, environmental resistance is essential; the adhesive must withstand storage conditions like humidity and temperature fluctuations without compromising its bond strength.
Another factor to consider is curing time; some adhesives require longer curing times than others, which can impact production efficiency. Furthermore, regulatory compliance is non-negotiable in the pharmaceutical industry; ensure that the chosen adhesive meets all safety standards and regulations applicable to your specific application. Lastly, ease of application can influence your choice—adhesives that are easier to apply may reduce labor costs and improve overall productivity.
What is the Best Adhesive to Bond Aluminum?
The question What is the best adhesive to bond aluminum? often arises in discussions about aluminum blister adhesives. While there isn't a one-size-fits-all answer due to varying application needs, polyurethane-based adhesives are frequently recommended for their excellent bonding properties with aluminum surfaces. They offer strong adhesion while providing flexibility that helps absorb stress during production and transport.
In addition to polyurethane options, epoxy adhesives are also popular for their superior durability and resistance to environmental factors like moisture or chemicals—making them ideal for long-term applications where product integrity is paramount. Ultimately, testing different formulations may be necessary to determine which adhesive performs best under specific conditions relevant to your product.
Comparing Adhesives for Specific Applications
When comparing adhesives for specific applications within aluminum blister packaging, it’s essential to look at performance metrics relevant to each scenario. For instance, if you’re dealing with PTP aluminum foil sealing in blister capsule packaging, a high-performance heat-sealable adhesive might be necessary for optimal results. This type of adhesive allows efficient sealing while maintaining a barrier against moisture or contaminants.
On the other hand, if you're working with alu alu versus traditional blister packs—what's the difference? Alu alu packs typically require stronger bonds due to their unique construction using two layers of aluminum foil instead of plastic films commonly found in standard blisters; thus requiring specialized adhesives designed specifically for this purpose. Each application has its nuances; therefore understanding these differences will guide you toward making informed decisions about which aluminum blister adhesive will best suit your needs.
Blister Capsule Packaging Techniques
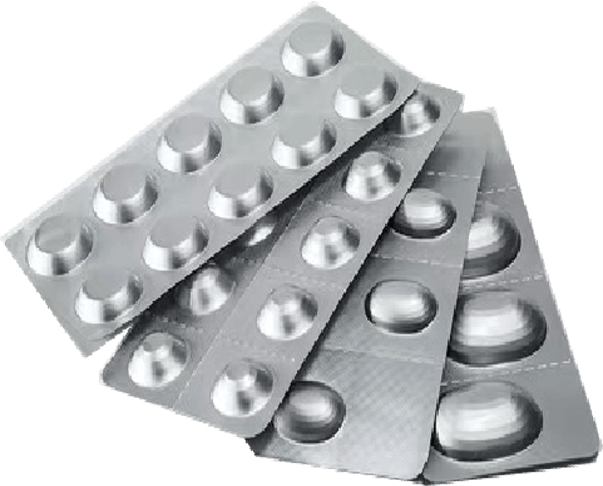
Blister capsule packaging has revolutionized the way pharmaceuticals are presented and protected, particularly through the use of PTP (Press-to-Peel) aluminum foil sealing. This technique involves using aluminum blister adhesive to bond the foil to a plastic base, effectively creating a barrier against moisture and light. As we delve into the specifics of this method, it’s essential to understand its advantages and innovations that continue to shape the industry.
Overview of PTP Aluminum Foil Sealing
PTP aluminum foil sealing is a widely adopted method in blister packaging that ensures optimal protection for capsules and tablets. It utilizes an aluminum blister adhesive that securely seals the medication within a cavity formed by a plastic base, typically made from PVC or PET. The process is efficient and reliable, allowing for easy access while maintaining product integrity.
The key components in this sealing process include high-quality aluminum foil, which serves as an effective barrier against environmental factors such as humidity and oxygen. This makes it crucial in preserving the efficacy of sensitive medications. Additionally, understanding what material is used for blister packaging helps manufacturers select appropriate substrates that enhance overall performance.
Benefits of Blister Capsule Packaging
Blister capsule packaging offers several benefits that make it an attractive option for pharmaceutical companies and consumers alike. Firstly, it provides excellent protection against external elements thanks to its robust design featuring aluminum blister adhesive that creates an airtight seal around each dose. This not only prolongs shelf life but also ensures dosage accuracy.
Another significant advantage is convenience; patients can easily access their medications without compromising safety or quality. Moreover, blister packs can be designed with child-resistant features, adding another layer of security for households with young children. The question often arises: What is the difference between alu alu and blister? While both types use aluminum materials for protection, alu alu typically features two layers of aluminum foil while traditional blisters usually have one layer combined with plastic.
Innovations in Blister Packaging Technology
The landscape of blister packaging technology continues to evolve with innovative solutions aimed at enhancing functionality and sustainability. Recent advancements include improved formulations of aluminum blister adhesive that provide stronger bonds while minimizing environmental impact through eco-friendly options like water-based resins from companies such as Chemix. These innovations not only meet regulatory standards but also align with growing consumer demand for sustainable practices.
Additionally, smart packaging technologies are emerging within this sector—integrating QR codes or NFC chips into blister packs allows manufacturers to provide patients with valuable information about their medications directly on their devices. Such innovations illustrate how traditional methods are being reimagined to cater to modern needs while ensuring safety and effectiveness remain paramount in pharmaceutical delivery systems.
Conclusion
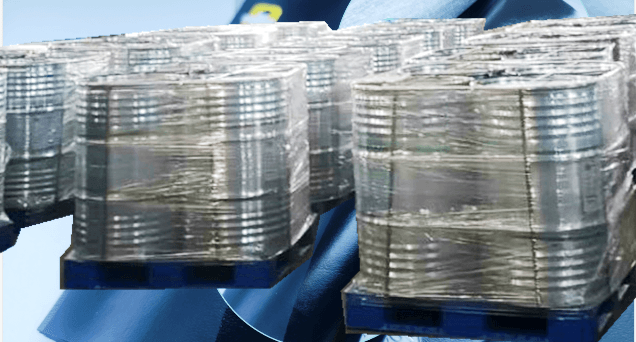
In wrapping up our exploration of aluminum blister packaging, it’s clear that this method offers a multitude of benefits that are hard to ignore. From ensuring the integrity of pharmaceutical products to enhancing user convenience, blister packaging stands out as a reliable choice. The role of aluminum blister adhesive is pivotal in maintaining these advantages, ensuring that the packaging remains secure and effective.
Recap of Blister Packaging Benefits
Blister packaging provides significant protection for its contents, safeguarding medications from environmental factors like moisture and light. One important aspect is understanding what material is used for blister packaging; typically, it includes PVC or PET combined with aluminum foil for optimal barrier properties. Moreover, the difference between alu alu and blister lies in their structure: alu alu uses two layers of aluminum for maximum protection while typical blister packs often use plastic backing.
Importance of Choosing the Right Adhesive
Selecting the right adhesive is crucial when considering what is the best adhesive to bond aluminum to aluminum; it can significantly influence both performance and product safety. The effectiveness of an aluminum blister adhesive not only impacts the package's integrity but also plays a vital role in regulatory compliance within the pharmaceutical industry. Therefore, understanding various factors such as curing time and environmental resistance can guide manufacturers toward making informed decisions about their adhesive choices.
Future Trends in Aluminum Blister Solutions
Looking ahead, innovations in blister capsule packaging are set to transform how we think about medication delivery systems. Advances in technology may lead to more sustainable materials being used alongside traditional options like PTP aluminum foil sealing, which enhances product shelf life while being eco-friendly. Furthermore, ongoing research into adhesives will likely yield new formulations that improve bonding performance without compromising safety or efficacy.