Introduction
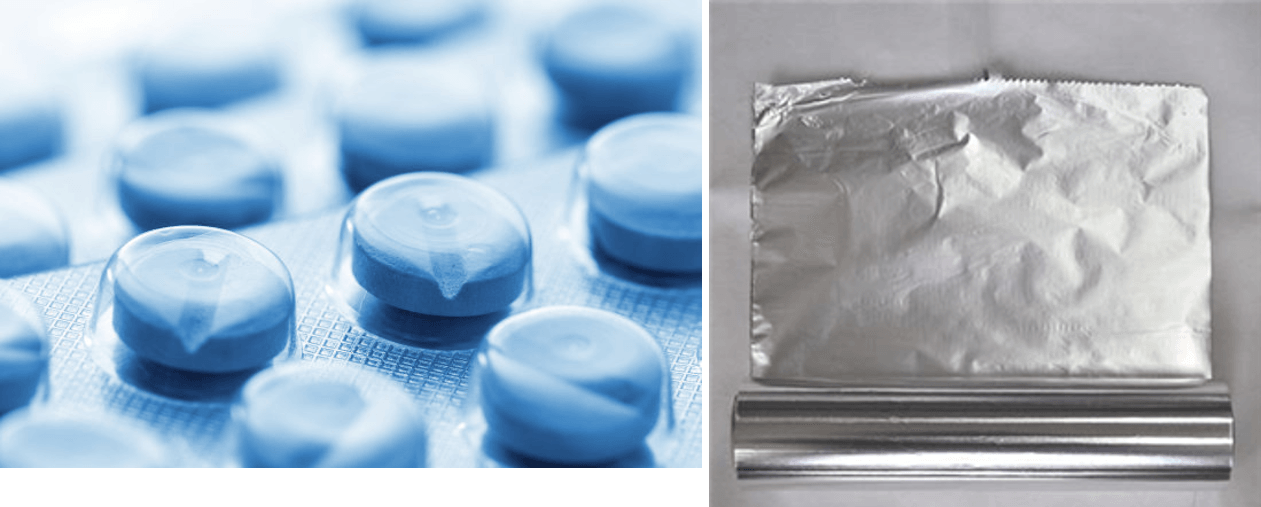
In the world of flexible packaging, heat seal coatings play a pivotal role in ensuring products remain secure and fresh. These coatings are designed to provide effective bonding and sealing, which is essential for various applications, from blister packaging to food and pharmaceutical uses. Understanding the mechanics behind heat seal coatings can significantly enhance product performance and sustainability.
Understanding Heat Seal Coatings
Heat seal coatings are specialized materials that create a strong bond when exposed to heat and pressure, making them indispensable in flexible packaging. They act as a barrier that not only seals products but also protects them from external factors such as moisture and contamination. By utilizing contact adhesives within these coatings, manufacturers can achieve reliable sealing while maintaining product integrity.
Importance in Flexible Packaging
The significance of heat seal coatings in flexible packaging cannot be overstated; they ensure that products arrive safely at their destination without compromising quality. In industries like food service and pharmaceuticals, where hygiene is paramount, these coatings provide an additional layer of protection against spoilage or contamination. Moreover, the versatility of heat seal technology enables its application across various substrates, enhancing its value across different sectors.
Key Benefits of Seal Coating
Seal coating offers numerous benefits that extend beyond mere functionality; it enhances the overall consumer experience by providing tamper-evident features and extending shelf life. The bonding achieved through heat seal processes ensures that packages remain intact during transport and handling, reducing waste due to damaged goods. Additionally, advancements in sustainable formulations mean that modern heat seal coatings can be both effective and environmentally friendly—an essential consideration for today’s eco-conscious consumers.
What are Heat Seal Coatings?
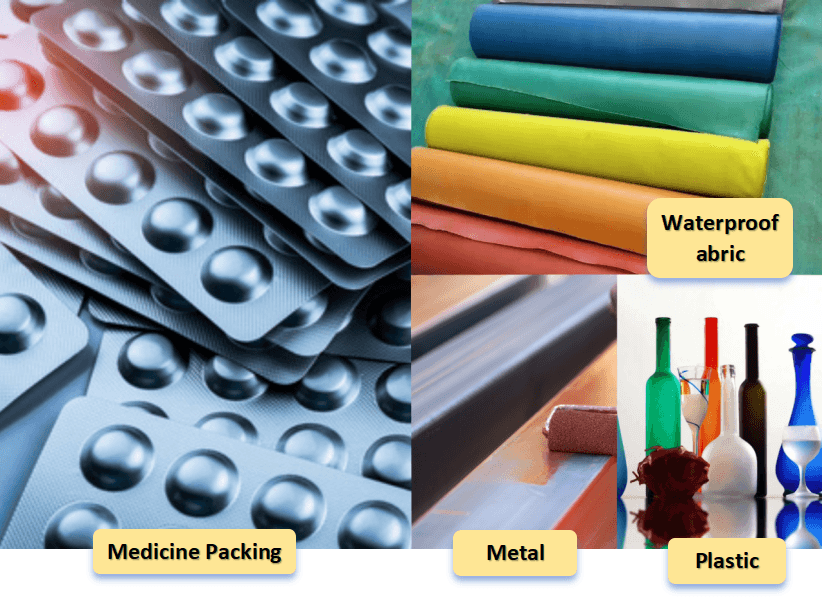
Heat seal coatings are specialized materials designed to create a strong bond when heat is applied, particularly in flexible packaging applications. These coatings enable the sealing of various materials, ensuring that products remain secure and protected from external elements. By facilitating effective bonding and sealing, heat seal coatings play a crucial role in enhancing the integrity of packaged goods.
Definition and Function
At its core, a heat seal coating is a layer applied to packaging substrates that activates under specific temperature conditions to form a bond between two surfaces. This function is essential for creating airtight seals that preserve freshness and prevent contamination in products like food and pharmaceuticals. In blister packaging, for instance, these coatings ensure that the contents remain secure while providing ease of access to consumers.
How They Work in Flexible Packaging
Heat seal coatings work by utilizing thermal energy to soften the coating material, allowing it to flow and bond with another surface upon cooling. During this process, the heat seal creates an effective barrier against moisture and air infiltration, which is vital for maintaining product quality over time. In flexible packaging scenarios, this mechanism enables manufacturers to produce reliable packages that withstand handling and transportation without compromising their contents.
Materials Used in Heat Seal Coatings
The composition of heat seal coatings can vary significantly based on their intended application; however, common materials include polymers such as polyethylene (PE), polypropylene (PP), and ethylene-vinyl acetate (EVA). These materials are chosen for their excellent bonding properties when heated alongside other substrates used in flexible packaging solutions. Additionally, contact adhesives may also be incorporated into some formulations to enhance adhesion properties further while ensuring optimal performance during sealing processes.
The Science Behind Heat Sealing
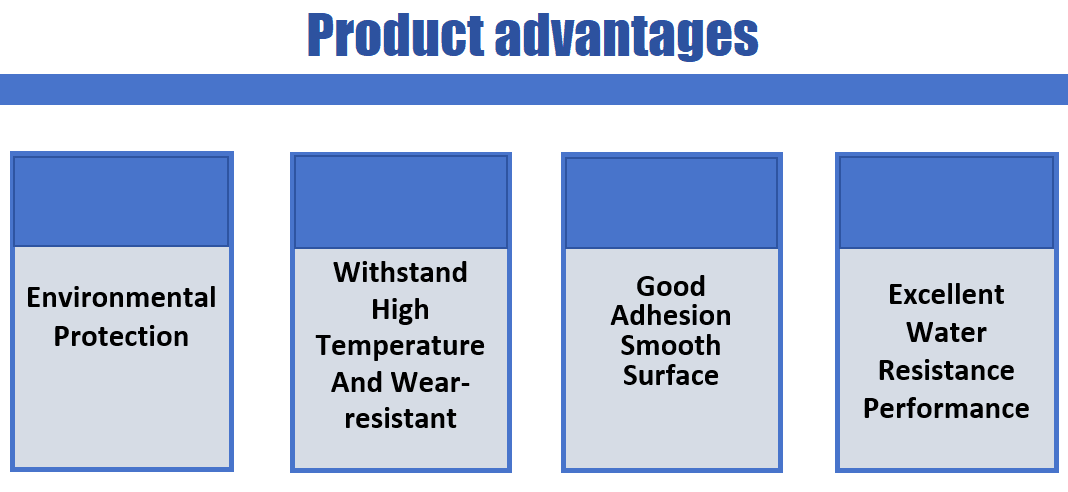
When it comes to heat seal coatings, understanding the underlying science is crucial for optimizing their use in flexible packaging. The process of heat sealing is not just about applying heat; it involves a sophisticated interplay of materials and techniques that ensure effective bonding and sealing. By grasping the thermal activation process, the bonding mechanism, and the role of contact adhesives, manufacturers can achieve better results in blister packaging and various other applications.
Thermal Activation Process
The thermal activation process is the heart of how heat seal coatings function. Essentially, this process involves applying controlled heat to activate the polymer layers within the seal coating, allowing them to flow and bond together effectively. Once heated to a specific temperature, these materials become pliable and create a strong bond upon cooling—an essential factor for reliable flexible packaging.
Temperature control is critical during this phase; too much heat can degrade the material while too little might result in weak seals. Understanding these nuances helps manufacturers avoid common pitfalls associated with improper application. Consequently, mastering this thermal activation process leads to improved performance in blister packaging and other sealed products.
Bonding Mechanism Explained
Understanding how bonding occurs during the sealing process sheds light on why heat seal coatings are so effective in flexible packaging applications. When two surfaces coated with a heat seal layer come into contact under pressure after being heated, they begin to intermingle at a molecular level—a phenomenon known as interfacial adhesion. This unique bonding mechanism allows for an incredibly strong seal that can withstand various stresses encountered during handling or transportation.
The effectiveness of this bonding relies heavily on factors such as temperature, pressure, and dwell time—the duration that surfaces are held together while cooling down. Achieving optimal conditions ensures that the bond formed is robust enough for demanding applications like food or medical packaging where integrity is paramount. Thus, understanding this bonding mechanism not only enhances product reliability but also boosts consumer confidence.
Role of Contact Adhesives
Contact adhesives play a pivotal role in enhancing the performance of heat seal coatings by providing additional layers of adhesion between substrates when necessary. These adhesives are particularly useful when dealing with challenging materials or when extra strength is required beyond what standard sealing can provide alone. They work synergistically with heat seals by ensuring that even under stress or environmental challenges, your blister packaging remains intact.
In many cases, incorporating contact adhesives into your flexible packaging solutions can lead to innovations that significantly improve product longevity and security against tampering or spoilage. However, it's essential to choose compatible adhesives that will not interfere with the thermal properties required for effective sealing—after all, no one wants an adhesive mishap ruining their carefully crafted package! Balancing these factors allows manufacturers to leverage both technologies effectively.
Applications of Heat Seal Coatings
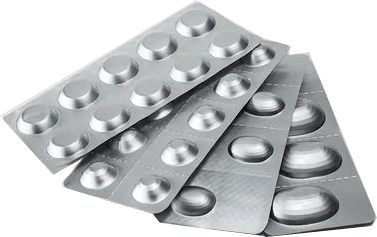
Heat seal coatings are revolutionizing various industries, particularly in flexible packaging. Their unique bonding and sealing capabilities make them indispensable for ensuring product integrity, safety, and freshness. From blister packaging to food and pharmaceutical solutions, the applications of heat seal coatings are vast and varied.
Blister Packaging Innovations
Blister packaging is one of the most exciting applications of heat seal coatings. This method not only protects products but also enhances shelf appeal through its clear visibility, thanks to the effective use of seal coating materials. Innovations in heat seal technology have led to improved bonding and sealing processes that ensure products remain secure while allowing manufacturers to use eco-friendly materials.
The versatility of heat seal coatings in blister packaging allows for customization based on specific product needs. Whether it's pharmaceuticals or consumer goods, these coatings provide a reliable barrier against moisture and contaminants, preserving product quality over time. With advancements in contact adhesives used in these applications, manufacturers can now achieve stronger bonds with lower energy costs.
Food Packaging Solutions
When it comes to food packaging solutions, heat seal coatings play a crucial role in maintaining food safety and extending shelf life. These coatings create airtight seals that prevent spoilage while preserving flavors and nutrients—an essential factor for both consumers and producers alike. The flexibility offered by these coatings allows for various types of food products to be packaged efficiently without compromising quality.
Moreover, the shift towards sustainable practices has led many companies to explore water-based heat seal options that reduce environmental impact without sacrificing performance. By using biodegradable materials alongside advanced sealing technologies, businesses can meet consumer demand for eco-friendly packaging while ensuring their products remain protected during transport and storage. The combination of innovative design and effective bonding makes heat seal coatings an ideal choice for any food manufacturer looking to enhance their packaging strategy.
Medical and Pharmaceutical Uses
In the medical field, where safety is paramount, heat seal coatings offer unparalleled reliability for packaging sensitive products like medications or surgical instruments. These specialized coatings ensure sterile environments by providing strong barriers against contaminants while allowing easy access when needed—a critical factor in healthcare settings where time is often of the essence. The consistent quality achieved through advanced bonding techniques ensures that health professionals can trust the integrity of their supplies.
Additionally, as regulations tighten around pharmaceutical packaging due to safety concerns, manufacturers are turning increasingly towards high-performance heat seal solutions that meet stringent standards without compromising efficiency or cost-effectiveness. The ability to customize these coatings further enhances their applicability across various medical devices and drug delivery systems—making them indispensable tools in modern healthcare practice. With continuous advancements in technology surrounding contact adhesives used within these applications, we can expect even more innovative uses for heat seal coatings going forward.
Chemix's Water-Based Resin Solution
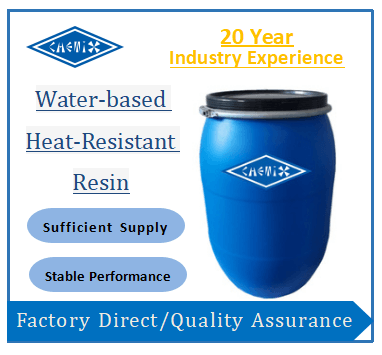
In the world of flexible packaging, Chemix’s water-based resin solution is making waves. This innovative approach to heat seal coatings not only meets industry demands but also prioritizes sustainability. By focusing on eco-friendly materials, Chemix is paving the way for a greener future in seal coating technology.
Sustainable and Environmentally Friendly
Chemix's water-based resin solution stands out due to its commitment to sustainability and environmental responsibility. Unlike traditional solvent-based coatings, which can release volatile organic compounds (VOCs) into the air, these water-based options minimize harmful emissions during production and application. This shift not only benefits manufacturers but also enhances consumer safety by reducing exposure to potentially harmful chemicals often associated with blister packaging and other flexible packaging solutions.
Moreover, this environmentally friendly approach aligns perfectly with global trends toward sustainable practices in various industries. By utilizing renewable resources and promoting recycling, Chemix’s heat seal coatings contribute positively to the circular economy. As consumers become more conscious of their choices, opting for products featuring sustainable seal coating solutions can enhance brand reputation while supporting ecological preservation.
Customization for Versatile Applications
One of the standout features of Chemix’s water-based resin solution is its customization potential for versatile applications across different sectors. Whether it’s blister packaging for pharmaceuticals or food packaging that requires specific barrier properties, these heat seal coatings can be tailored to meet diverse needs effectively. This flexibility ensures that clients receive a product that aligns perfectly with their bonding and sealing requirements.
Customization doesn’t just stop at formulation; it extends to performance characteristics as well. For instance, varying thicknesses, adhesion strengths, and curing times can be adjusted based on specific application demands—making these coatings incredibly adaptable in the fast-paced world of flexible packaging. With such versatility at hand, businesses can confidently tackle unique challenges while maintaining high-quality standards.
Performance vs. Traditional Solvents
When comparing performance between Chemix's water-based resin solution and traditional solvent-based systems, it's clear that advancements have been made in heat seal technology. The bonding mechanisms employed by these innovative coatings are designed to provide excellent adhesion without compromising flexibility or durability—essential factors in effective flexible packaging solutions like blister packs or food wraps. Consequently, manufacturers no longer have to choose between performance and environmental responsibility; they can enjoy both with modern seal coating options.
Furthermore, testing has shown that these water-based formulations exhibit comparable or even superior performance metrics when matched against their solvent counterparts under various conditions—temperature fluctuations included! This means businesses can confidently transition from conventional methods without sacrificing quality or efficiency in their production processes. As industries continue evolving towards greener practices, embracing such advancements will undoubtedly give companies a competitive edge while fostering sustainable growth.
Challenges and Considerations
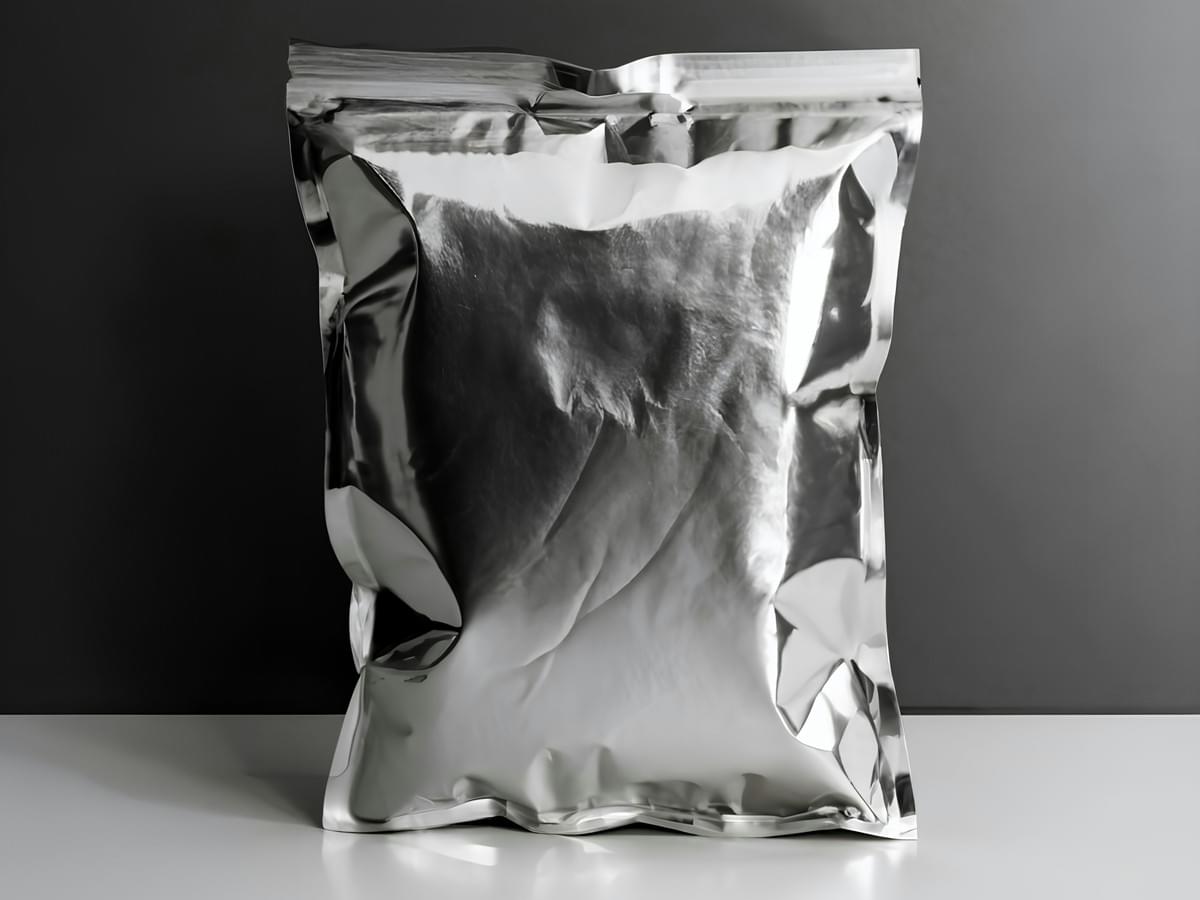
When it comes to heat seal coatings, navigating the landscape of options can feel like a maze. Selecting the right type for your needs is crucial, as different applications require specific properties. Whether you're working with blister packaging, food packaging, or medical applications, understanding the nuances of seal coating can make all the difference in achieving optimal bonding and sealing.
Selecting the Right Type for Your Needs
The first challenge in working with heat seal coatings is identifying which type best suits your application. Various formulations exist depending on factors such as substrate compatibility, desired seal strength, and environmental conditions. For instance, if you’re dealing with blister packaging that requires clear visibility of contents while maintaining an airtight seal, choosing a transparent heat seal coating designed for this purpose will be essential.
Additionally, consider whether you need a permanent bond or a peelable one; this decision will directly influence your choice of contact adhesives used alongside your heat seal coatings. It’s also wise to consult with manufacturers who specialize in flexible packaging to ensure you’re not just picking any random option off the shelf but one that aligns perfectly with your performance expectations.
Temperature and Pressure Variables
Temperature and pressure are pivotal when applying heat seal coatings; they can make or break the effectiveness of your sealing process. Each type of coating has its own optimal temperature range for activation—exceeding these limits could lead to scorching or poor adhesion results. Similarly, insufficient pressure may result in incomplete bonding between layers, ultimately compromising product integrity.
Understanding these variables allows you to fine-tune your processes for maximum efficiency and effectiveness in bonding and sealing applications. Always conduct preliminary tests under controlled conditions before scaling up production; this practice ensures that you achieve consistent results across various batches without unexpected surprises down the line.
Common Mistakes in Application
Even seasoned professionals can stumble into common pitfalls when applying heat seal coatings—don’t let that be you! One frequent mistake is neglecting surface preparation; contaminants like dust or grease can drastically affect adhesion quality and lead to failures during use. Ensuring surfaces are clean and appropriately treated beforehand is key to achieving strong bonds.
Another common oversight involves miscalculating the required time for heating; rushing through this step often results in weak seals that won’t hold up under stress. Lastly, failing to monitor equipment calibration regularly may lead to inconsistent application thicknesses—this inconsistency can cause variability in performance across different production runs.
Conclusion
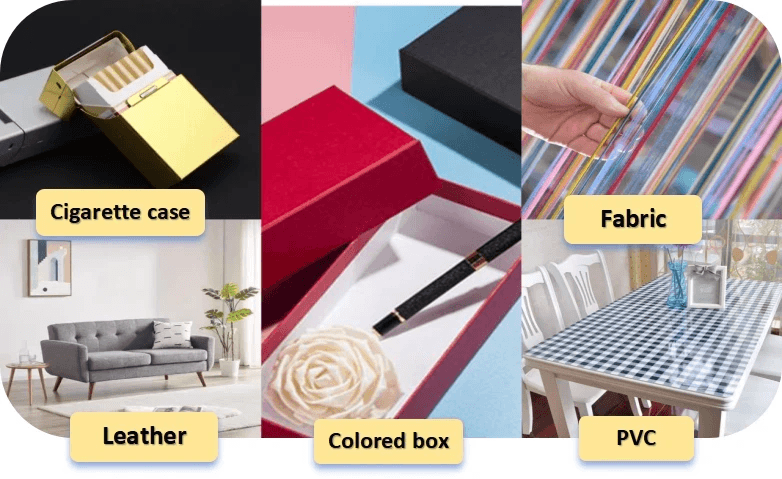
In the ever-evolving world of flexible packaging, heat seal coatings are becoming increasingly vital for ensuring product integrity and consumer safety. As industries adapt to new technologies and sustainability goals, the importance of understanding these coatings cannot be overstated. With their ability to provide reliable bonding and sealing solutions, they are set to play a crucial role in the future of packaging.
Future Trends in Heat Seal Coatings
The future of heat seal coatings looks promising, with advancements in materials science leading to enhanced performance characteristics. Innovations such as improved thermal activation processes will enable better bonding in blister packaging applications, ensuring that products remain secure yet easy to open. Additionally, as manufacturers continue to prioritize efficiency and sustainability, we can expect a shift toward more eco-friendly seal coating solutions that meet both regulatory standards and consumer expectations.
Enhancing Sustainability in Packaging
Sustainability is no longer just a buzzword; it's a necessity in modern packaging solutions. Heat seal coatings are evolving to incorporate sustainable materials that reduce environmental impact while maintaining high performance standards. By opting for water-based resins and minimizing reliance on traditional solvents, companies can enhance their commitment to eco-friendly practices without compromising on the effectiveness of their bonding and sealing capabilities.
Choosing the Right Coating for Performance
Selecting the right heat seal coating involves careful consideration of various factors including application type, temperature requirements, and specific material interactions. Different industries may require unique properties from their seal coatings—what works best for blister packaging might not be suitable for food or medical applications. Understanding these nuances will empower businesses to make informed decisions that optimize performance while ensuring product safety.