Introduction
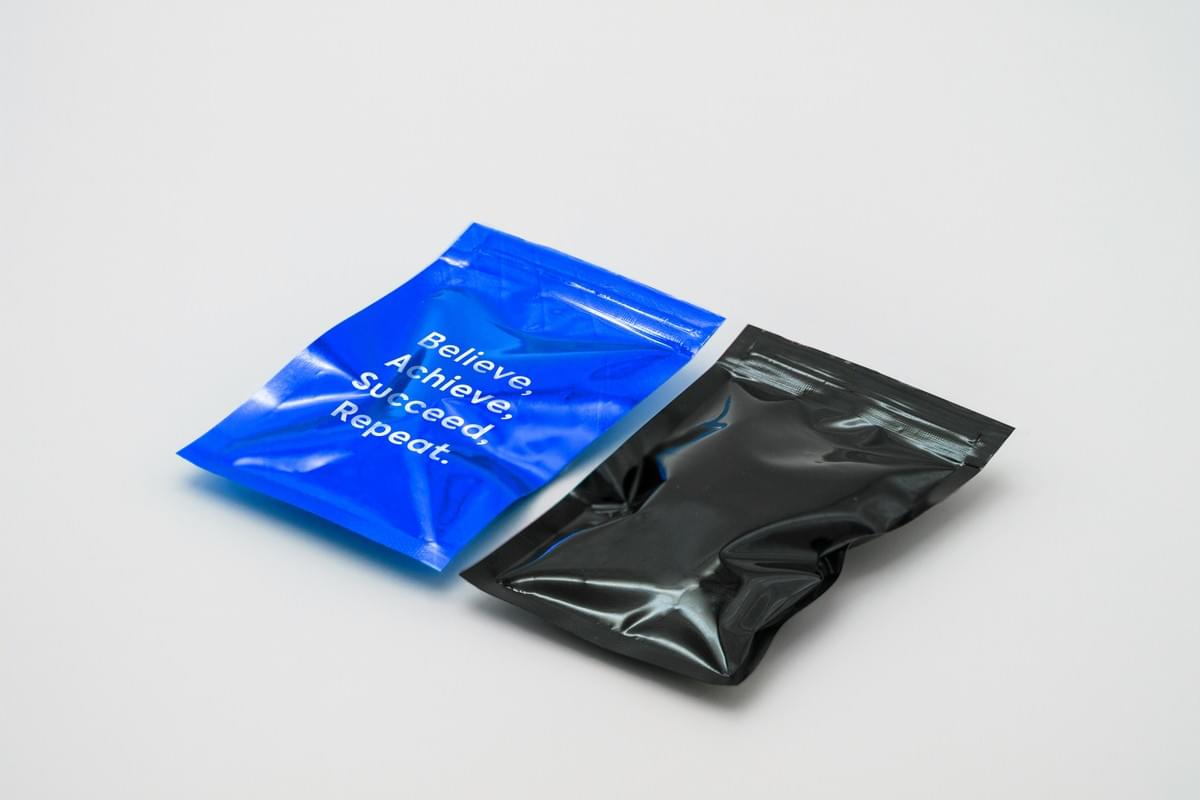
In the world of flexible packaging, adhesive coating methods play a pivotal role in ensuring that products not only look good but also stay intact during transport and storage. Understanding how these adhesives work is essential for anyone involved in packaging design or production. The right adhesive film can make all the difference, affecting everything from product shelf life to consumer experience.
Understanding Flexible Packaging Adhesives
Flexible packaging adhesives are specially formulated substances that bond various materials together, providing strength and flexibility to the final product. These adhesives come in various types, including hot melt, solvent-based, and water-based options, each with unique properties suited for different applications. By grasping the nuances of these adhesive coating methods, manufacturers can optimize their packaging solutions for efficiency and sustainability.
Importance of Coatings in Packaging
Coatings are crucial in packaging as they enhance both functionality and aesthetics while offering protection against environmental factors such as moisture and oxygen. A well-chosen coating not only improves adhesion but also contributes to the overall durability and performance of the package. Therefore, understanding the importance of coatings is vital for achieving high-quality results in flexible packaging applications.
Choosing the Right Adhesive Coating
Selecting the appropriate adhesive coating can be a daunting task given the myriad options available on the market today. Factors such as material compatibility, application method, and intended use must all be taken into account when making this decision. Ultimately, choosing the right adhesive film ensures that your packaging meets industry standards while appealing to consumers’ desires for sustainability and functionality.
Types of Adhesive Coating Methods
Overview of Common Techniques
In the realm of adhesive coating methods, several techniques stand out for their effectiveness and versatility. Common approaches include gravure, flexography, and slot die coating, each offering unique advantages depending on the application at hand. These methods allow for precise control over film thickness and uniformity, ensuring that the adhesive surface meets specific performance criteria.
Gravure printing is particularly popular for high-speed applications due to its ability to handle intricate designs with ease. Flexographic printing shines in environments where quick drying times are essential, making it a go-to choice for food packaging. Slot die coating offers precision that is hard to beat when uniformity is paramount—perfect for creating an ideal adhesive film layer.
Comparing Hot Melt and Solvent-Based Coatings
When diving into adhesive coating methods, hot melt and solvent-based coatings often come up in discussions regarding performance and application ease. Hot melt adhesives are solid at room temperature but become tacky upon heating; they offer rapid setting times and excellent adhesion properties without solvents that could complicate processes or impact health regulations. On the other hand, solvent-based coatings utilize volatile organic compounds (VOCs) that evaporate during curing but may raise environmental concerns due to emissions.
While hot melts provide strong initial adhesion and are less likely to warp substrates, solvent-based options can achieve a smoother finish on surfaces requiring a more refined appearance. The choice between these two often boils down to specific project requirements—whether speed or finish quality takes precedence will guide manufacturers toward their ideal solution in adhesive films or surface coatings.
Benefits of Water-Based Adhesive Coating
Water-based adhesive coatings have emerged as champions in sustainable practices within flexible packaging industries—offering numerous benefits without sacrificing performance. One significant advantage is their eco-friendliness; these adhesives contain fewer harmful solvents compared to traditional options, making them safer for both users and the environment alike. Additionally, water-based systems typically exhibit lower VOC levels while still providing robust adhesion properties across various surfaces.
Another perk of using water-based adhesives lies in their versatility—they can be tailored for different applications such as film coating or bonding various materials together seamlessly without compromising quality or durability. Notably, they also allow for easier cleanup compared to solvent-based counterparts since water serves as a primary carrier during application processes. This makes them an attractive option not only from an environmental standpoint but also from a practical one.
In summary, whether you're exploring hot melt versus solvent-based coatings or leaning towards eco-friendly options like water-based adhesives, understanding these adhesive coating methods can significantly impact your final product's success in today's competitive market landscape.
Selecting the Right Adhesive Film
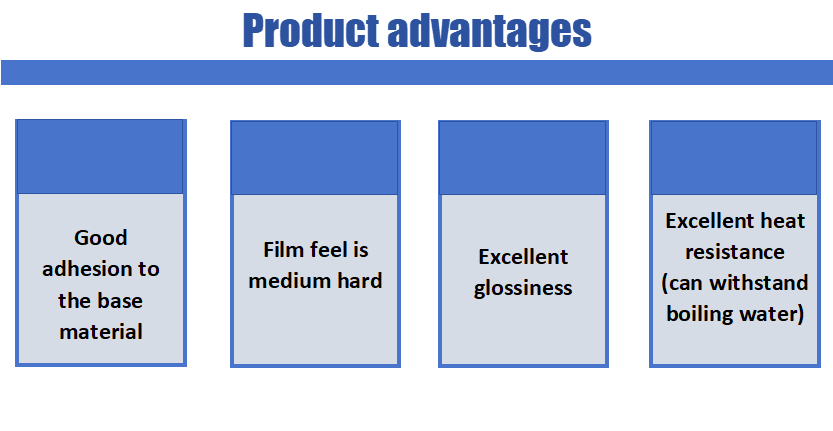
Choosing the right adhesive film is crucial for ensuring optimal performance in flexible packaging applications. The selection process involves a careful evaluation of various factors, including the specific requirements of your project, compatibility with adhesive coating methods, and the intended use of the final product. Understanding these elements can help you make informed decisions that enhance both functionality and sustainability.
Key Considerations for Your Project
When selecting an adhesive film, start by identifying the primary requirements of your project. Factors such as temperature resistance, moisture barriers, and compatibility with different adhesive coating methods should guide your decision-making process. Additionally, consider how the chosen adhesive surface will interact with other materials in your packaging to ensure a seamless bond and reliable performance.
Another critical consideration is regulatory compliance—especially for food and beverage applications—where safety standards must be met. Assessing environmental impact is also vital; opting for eco-friendly options can enhance your brand's reputation while contributing to sustainable practices in packaging. Lastly, don’t forget about cost-effectiveness; balancing quality with budget constraints can lead to a successful outcome.
Popular Adhesive Film Options
There are several popular adhesive film options available on the market today that cater to various needs and applications. Polyethylene (PE) films are widely used due to their flexibility and excellent sealing properties, making them ideal for food packaging where freshness is paramount. Polyester (PET) films offer superior strength and durability, often preferred for products requiring high-performance attributes.
For more specialized needs, consider polyvinyl chloride (PVC) films that provide excellent clarity and gloss but may raise environmental concerns due to their production processes. Biodegradable films are gaining traction as sustainable alternatives; they provide similar performance levels while minimizing environmental impact. Each option has unique properties affecting adhesion levels when paired with different adhesive coating methods.
How Adhesive Film Impacts Performance
The choice of adhesive film significantly impacts overall performance in flexible packaging solutions—affecting everything from seal integrity to shelf life of packaged goods. A well-selected adhesive surface ensures strong bonding between layers while preventing delamination during handling or transportation processes. This not only enhances product protection but also improves user experience by maintaining product quality.
Moreover, certain films can enhance barrier properties against moisture or gases when combined with appropriate film coating techniques—ultimately prolonging shelf life for perishable items like snacks or beverages. The right combination of adhesive film and surface coating not only optimizes functionality but also contributes to aesthetic appeal through clarity or printability features that attract consumers' attention on store shelves.
In conclusion, understanding how different types of adhesive films interact with various adhesives will empower you to make informed choices that elevate your packaging solutions while considering sustainability goals.
Film Coating in Flexible Packaging
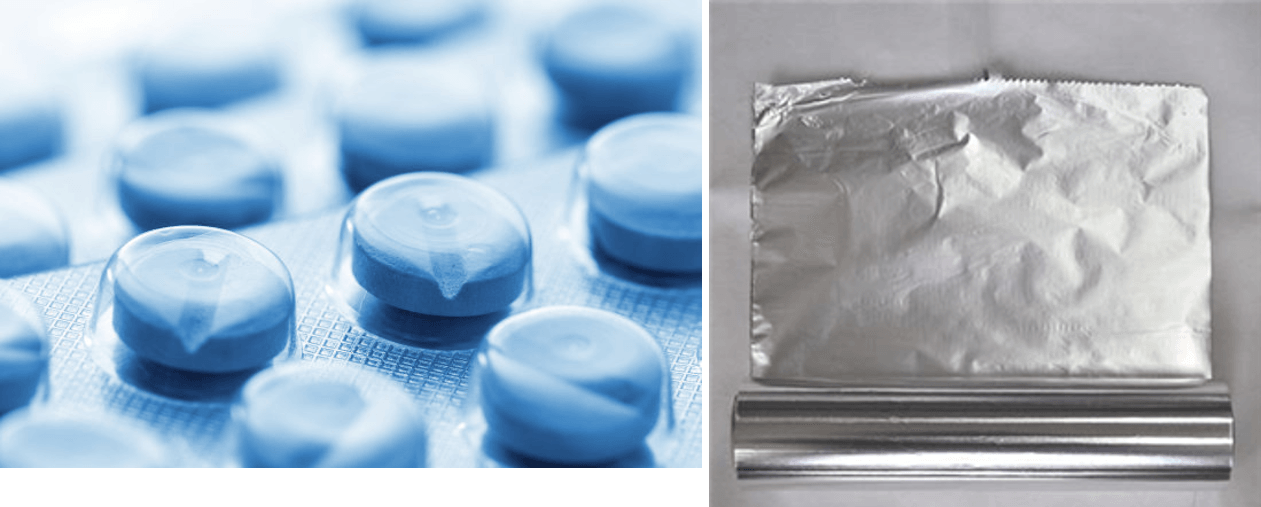
In the world of flexible packaging, film coating plays a pivotal role in enhancing product performance and longevity. This technique involves applying a thin layer of material to a substrate, creating an adhesive surface that improves barrier properties and adhesion. By utilizing various adhesive coating methods, manufacturers can tailor the film to meet specific requirements for different applications.
What is Film Coating?
Film coating is a process where a polymer-based layer is applied to surfaces to improve their functionality and aesthetics. This method not only enhances adhesion but also provides protection against moisture, oxygen, and other environmental factors that can compromise product integrity. The versatility of film coating makes it an essential component in various industries, particularly in flexible packaging.
Applications in Food and Beverage
In the food and beverage sector, film coating has become indispensable for maintaining freshness and extending shelf life. Adhesive films are commonly used for packaging snacks, beverages, and ready-to-eat meals, ensuring they remain uncontaminated by external elements. The right adhesive coating methods allow manufacturers to create packages that are not only functional but also visually appealing to consumers.
Advantages of Film Coating
The advantages of film coating extend beyond mere aesthetics; they significantly enhance product performance as well. First off, these coatings provide superior barrier properties that protect against moisture and oxygen infiltration, which is critical for food preservation. Additionally, using innovative adhesive surface treatments can lead to improved adhesion strength between layers, resulting in more durable packaging solutions that stand the test of time.
Surface Coating Techniques
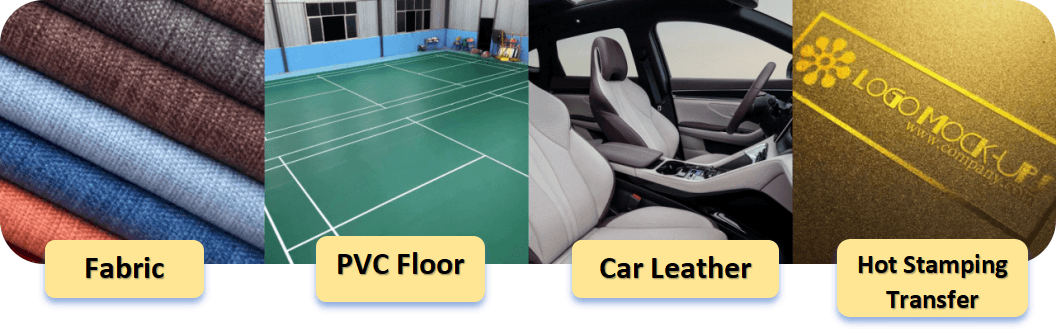
Surface coating techniques play a pivotal role in enhancing the performance and longevity of flexible packaging. These methods are essential for ensuring that adhesive coatings adhere effectively to various substrates, providing a robust barrier against environmental factors. By employing innovative surface treatments, manufacturers can optimize their adhesive films for specific applications, resulting in improved product quality.
Essential Methods for Surface Treatment
When it comes to surface treatment, several essential methods stand out in the world of adhesive coating methods. Plasma treatment is one such technique that modifies the surface energy of materials, making them more receptive to adhesive films. Another popular method is flame treatment, which utilizes high temperatures to clean and activate surfaces, ensuring optimal adhesion for subsequent coatings.
Chemical treatments also play a crucial role in surface preparation by applying primers or adhesion promoters that enhance bonding strength between the substrate and the adhesive coating. Each of these techniques contributes uniquely to achieving superior adhesion and performance characteristics in flexible packaging applications. Ultimately, selecting the right surface treatment method can significantly influence the effectiveness of your chosen adhesive film.
Enhancing Adhesion and Durability
Enhancing adhesion and durability is paramount when considering various surface coating techniques within flexible packaging solutions. Properly treated surfaces ensure that adhesive coatings bond effectively, reducing the risk of delamination or failure during use. This durability is particularly important in food packaging where maintaining product integrity is vital.
Moreover, advancements in adhesive technology have led to formulations that improve resistance against moisture and chemicals—factors critical for preserving contents over time. By focusing on enhancing adhesion through effective surface treatments, manufacturers can create long-lasting products that meet consumer demands without compromising quality or safety.
Innovations in Surface Coating
The landscape of surface coating is continually evolving with innovative approaches aimed at improving performance metrics across various industries. Recent advancements include nanotechnology-based coatings that offer superior properties such as scratch resistance and antimicrobial effects—ideal for applications like food packaging where hygiene is paramount. These innovations not only enhance functionality but also contribute to sustainability by reducing material usage through more efficient processes.
Furthermore, smart coatings equipped with sensors are making waves by providing real-time feedback on product integrity during storage and transport—an exciting development for supply chain management! As we look ahead, it's clear that ongoing research into new materials and techniques will further refine our understanding of how effective adhesive coating methods can be applied across different sectors.
Chemix's Water-Based Resin Solution
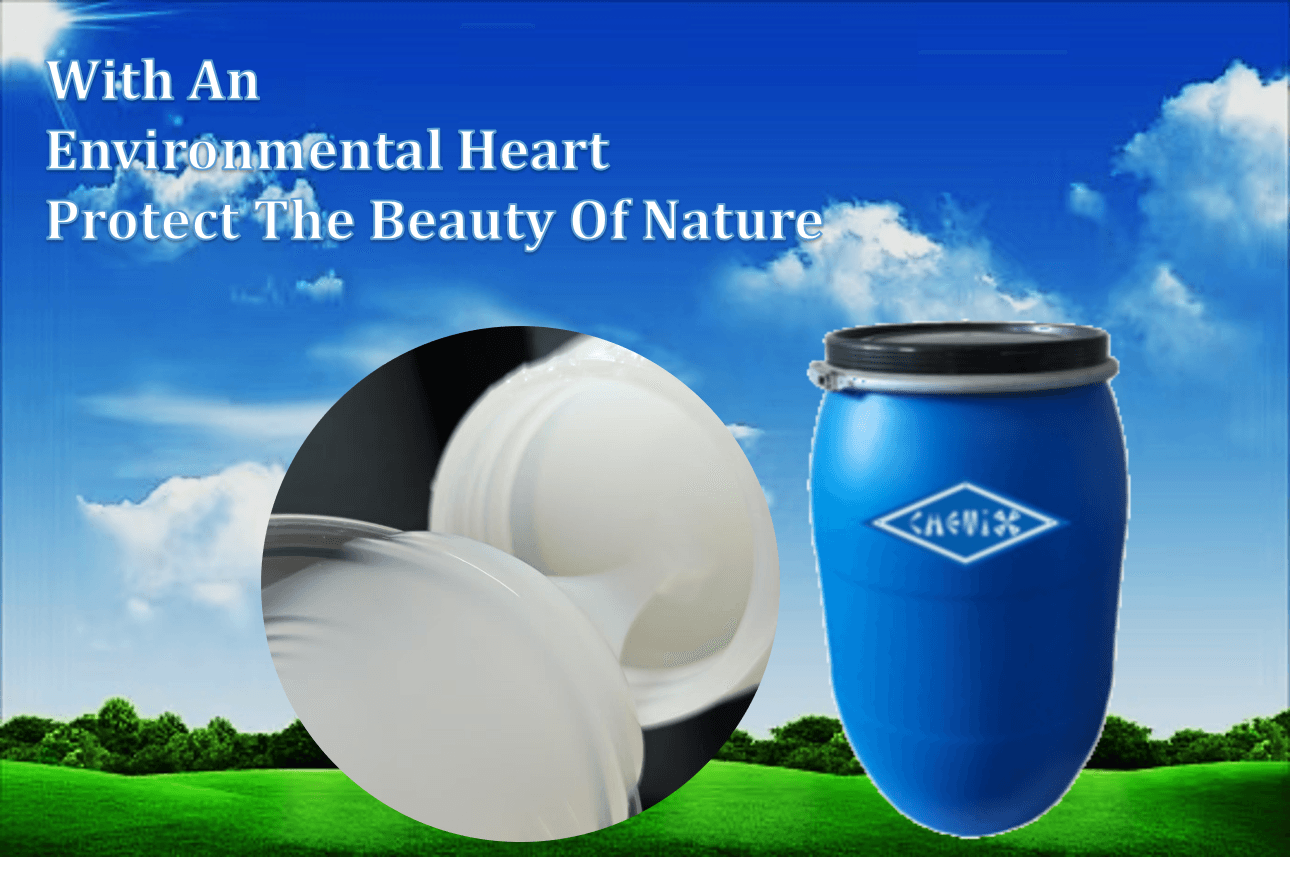
Chemix's water-based resin solution stands out as a beacon of innovation in the realm of adhesive coating methods. These resins are not only designed to perform but also to protect our environment, making them a favorite among eco-conscious manufacturers. By opting for water-based formulations, companies can significantly reduce their carbon footprint while still achieving high-quality adhesion and coating performance.
Eco-Friendly Advantages of Water-Based Resins
The eco-friendly advantages of water-based resins are numerous and compelling. First off, these resins emit significantly lower levels of volatile organic compounds (VOCs) compared to their solvent-based counterparts, contributing to better air quality both indoors and outdoors. Additionally, water-based adhesives often use renewable resources in their formulation, aligning with the growing demand for sustainable practices in packaging industries.
Another key advantage is the ease of cleanup associated with water-based products; they can be washed away with just soap and water, minimizing waste and cleanup costs. When it comes to safety, these resins pose fewer health risks during application, making them ideal for use in sensitive environments like food packaging. Ultimately, choosing water-based options not only enhances the adhesive surface properties but also supports a more sustainable future.
Applications in Adhesives and Coatings
Water-based resins find diverse applications across various adhesive coating methods and sectors. In flexible packaging, they serve as effective bonding agents that enhance the performance of adhesive films used for sealing bags or laminating materials. Their versatility extends into industries like automotive and construction, where they contribute to durable surface coatings that withstand harsh conditions.
In food and beverage packaging specifically, these resins ensure compliance with stringent safety regulations while providing excellent barrier properties against moisture and contaminants. This makes them an ideal choice for maintaining product freshness without compromising on sustainability goals. The adaptability of Chemix's water-based solutions allows companies to explore innovative uses across multiple sectors while ensuring reliability in adhesion.
Customization for Specific Needs
One size doesn’t fit all when it comes to adhesive film solutions; customization is key! Chemix understands that every project has unique requirements—whether it’s specific adhesion strength or compatibility with certain substrates—and offers tailored formulations accordingly. This level of customization ensures that manufacturers can achieve optimal results based on their specific needs without sacrificing performance.
Moreover, Chemix collaborates closely with clients throughout the development process to fine-tune properties such as viscosity or drying time based on application demands. This attention to detail not only improves overall efficiency but also enhances product quality by ensuring that each adhesive coating method is perfectly suited for its intended use case. With customized solutions at hand, businesses can confidently tackle challenges in flexible packaging while remaining committed to sustainability.
Conclusion
As we draw our discussion on adhesive coating methods to a close, it's clear that the right choice can make or break your packaging project. The diversity of adhesive coatings—from water-based to solvent-based—offers a range of options tailored to specific needs and applications. Understanding these methods not only enhances product performance but also contributes to sustainable practices in the packaging industry.
Final Thoughts on Adhesive Coating Methods
When navigating the realm of adhesive coating methods, one must consider factors such as environmental impact, application technique, and end-use requirements. Each method presents unique benefits and challenges, making it crucial for manufacturers to evaluate their specific needs thoroughly. Ultimately, selecting the right adhesive coating is essential for ensuring product integrity and customer satisfaction.
Key Takeaways on Adhesive Films
Adhesive films are pivotal in achieving optimal bonding in flexible packaging solutions. Whether you're opting for a high-performance film or a more eco-friendly option, understanding the properties of different adhesive films will guide you toward better choices. Remember that the performance of your packaging hinges significantly on these films; they are not just an afterthought but rather an integral component of your overall design strategy.
The Future of Sustainable Packaging Solutions
The future looks bright for sustainable packaging solutions as innovations continue to emerge in adhesive coatings and films alike. With growing consumer demand for environmentally friendly products, manufacturers are encouraged to explore water-based adhesives and other eco-conscious options that minimize environmental impact without sacrificing quality. As we move forward, embracing these advancements will be key to creating effective and responsible packaging that meets both market demands and sustainability goals.